In questo articolo esploriamo tre esempi di ottimizzazione riguardanti un'azienda manifatturiera, un’azienda agricola e una ditta specializzata in ambito meccanico. Ognuno di questi casi ha come protagonista aziende che hanno affrontato varie sfide, e che sono riuscite a migliorare i loro processi adottando le soluzioni proposte.
Il case study dell’azienda manifatturiera
Specializzata nella fabbricazione di metalli su misura, questa impresa fa parte di una nicchia nel mondo della produzione. Con un numero totale di 15 dipendenti, è riuscita a crearsi una reputazione per la fornitura di prodotti metallici di alta qualità e su misura per le esigenze della propria clientela.- Problemi emersi
Il secondo problema era invece inerente alla programmazione della produzione. Di fatto, venendo fatta manualmente, causava diverse inefficienze. Il risultato era un sottoutilizzo delle risorse e un mancato rispetto delle scadenze.
Un terzo e ultimo problema, comune nelle imprese di piccole o medie dimensioni, era il flusso di informazioni tra i diversi reparti. Essendo lento e spesso soggetto a fraintendimenti, causava ritardi ed errori nella gestione delle commesse.
- Soluzioni proposte
Attraverso la mappatura dei processi aziendali è stato possibile delineare una ‘panoramica a 360 gradi’ dello stato attuale aziendale.
Sulla base della mappatura dei processi produttivi, è stato implementato un sistema software di gestione dell'inventario, in modo da rendere possibile il tracciamento dei materiali in tempo reale, e consentendo una migliore controllo della merce presente in magazzino.
Per risolvere i problemi riguardanti la produzione è stato invece introdotto un software di pianificazione della produzione come supporto nella gestione degli ordini e della loro programmazione, tenendo conto della priorità e della disponibilità dei materiali.
È stato poi rivisto il processo riguardante la comunicazione delle informazioni. Acquisendo consapevolezza sull’iter comunicativo, è stato possibile implementare delle best practices per permettere di informare tempestivamente riguardo qualsiasi modifica o aggiornamento.
- Analisi a tre mesi dall'intervento
I tassi di consegna puntuale sono aumentati del 15% e l'utilizzo delle macchine è migliorato del 30%, con conseguente aumento della produttività.
Inoltre, le nuove regole per la comunicazione di informazioni hanno ridotto gli errori e le incomprensioni del 40%, favorendo nel mentre anche un ambiente di lavoro più collaborativo.
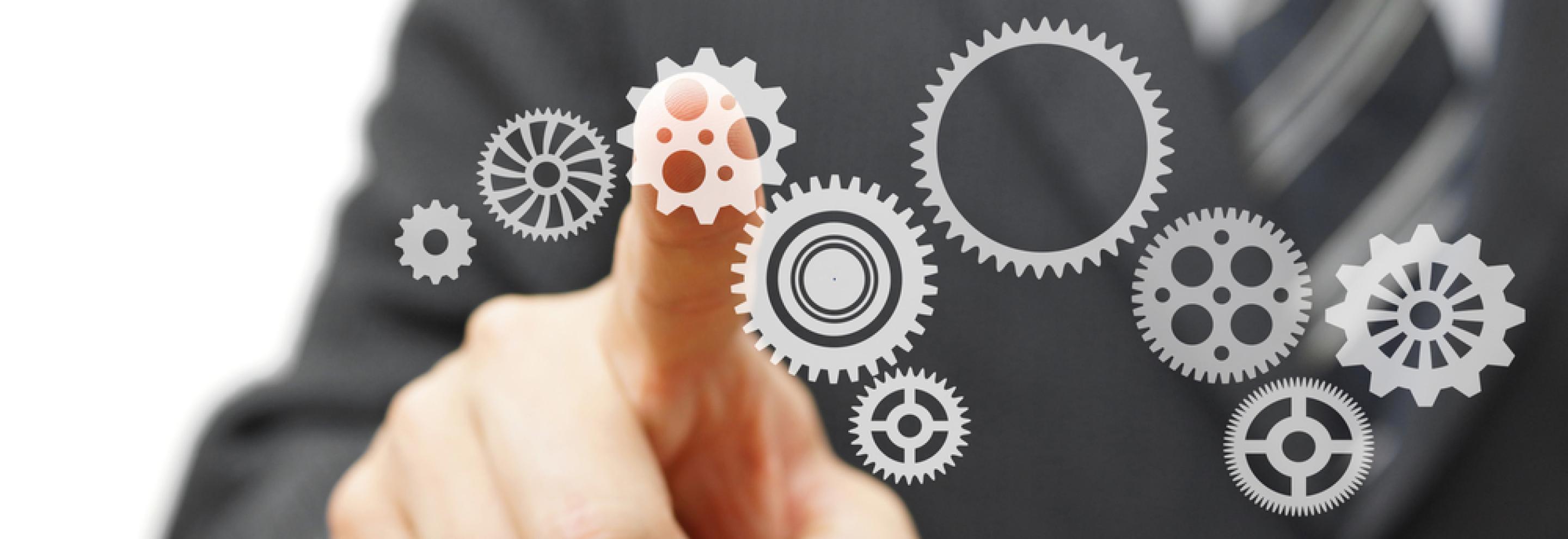
Il case study della azienda agricola
Il secondo caso ci porta nel mondo della produzione vinicola. L’azienda è composta da 8 persone in produzione e 5 in ufficio.- Problemi incontrati
Durante la consulenza è stato poi notato che si vendeva l’uva a causa di una mancanza di spazio e di capacità produttiva. I dati emersi hanno infatti evidenziato che nei tre anni precedenti, se si fosse optato per la trasformazione in vino invece che sulla vendita d’uva, l’azienda avrebbe guadagnato fino al 90% del possibile fatturato. È stata quindi condotta un’ulteriore analisi in modo da aumentare spazio e capacità produttiva e massimizzare il profitto grazie ad un aumento della capacità produttiva.
- Soluzioni proposte
Come prima cosa, è stato introdotto un cambio di metodo in modo da liberare una persona dall’area produttiva, destinandola ad attività a maggior valore aggiunto e andando ad aumentare di conseguenza l’efficienza in produzione del 20%.
Sono stati creati vari scenari con possibili investimenti necessari per sviare il problema del poco spazio e della bassa capacità produttiva, ed è stata scelta insieme alla direzione l’opzione più adatta alle esigenze aziendali.
- Analisi a tre mesi dall'intervento
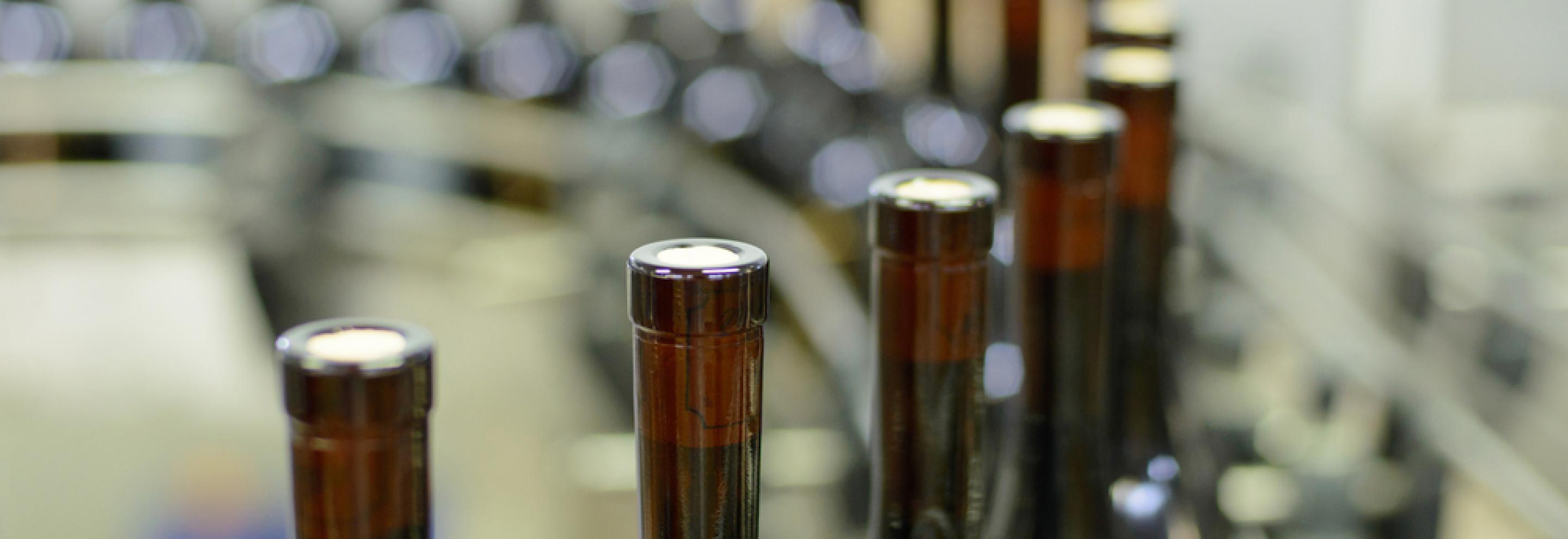
Il case study della ditta specializzata in ambito meccanico
- Problemi incontrati
Era necessario affrontare un ulteriore problema, relativo al tempo ciclo di una macchina, che, essendo molto lungo, portava ad uno stato di inattività di un operatore.
- Soluzioni proposte
Grazie ai risultati dell’analisi tempi e metodi sui micromovimenti, si è potuto comprendere come agire sul tempo ciclo, e migliorare il lavoro degli operatori dal punto di vista ergonomico. Con questo obiettivo sono stati introdotti dei pallet che trasportano materie prime, in modo da intervenire appunto sul miglioramento ergonomico.
È stato ripensato completamente il layout della postazione di circa 25 metri quadri. Questo ha permesso di passare da un tempo ciclo di 35 minuti a uno di 20 minuti senza fare investimenti, quindi a costo zero.
Con un’analisi delle tempistiche relativa alle altre lavorazioni che avvengono all’interno della fabbrica è stato creato un abbinamento ‘operatore-macchina’, permettendo così di recuperare il 50% di ore lavorative di ogni operatore, in modo da impiegarle in altre attività a maggior valore aggiunto.
- Analisi a 3 mesi dall'intervento
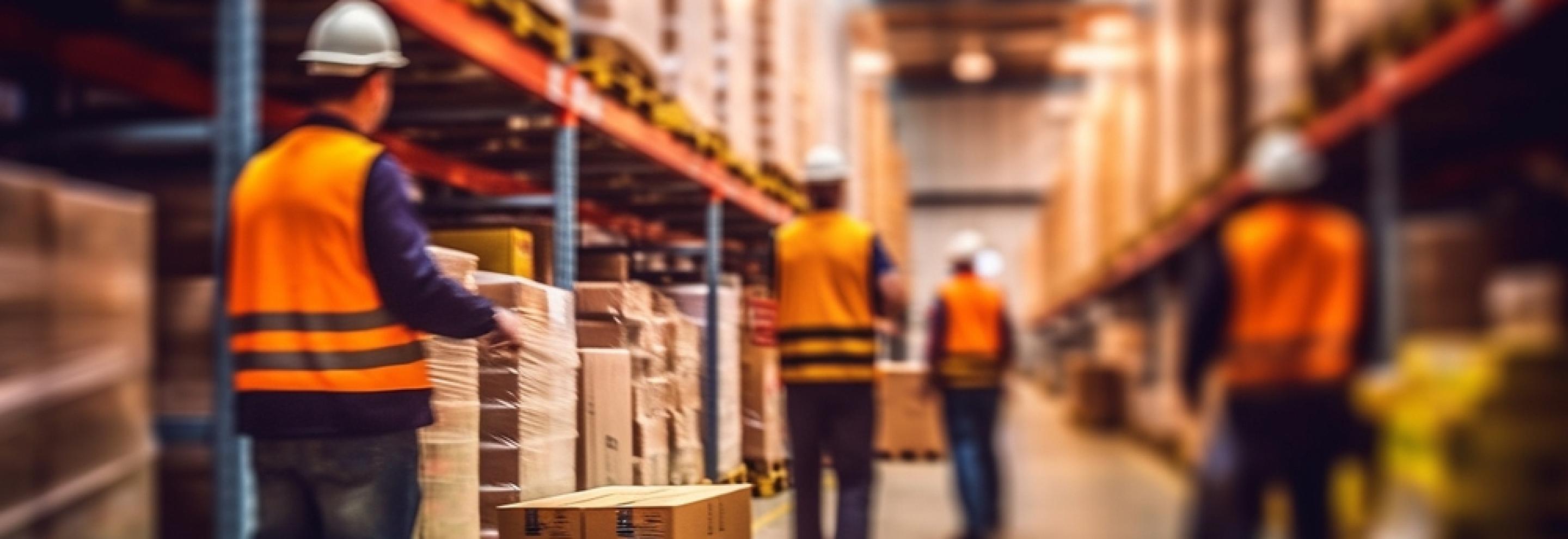
Conclusione
Nel mondo delle imprese, la ricerca dell'efficienza e della redditività non finisce mai.Questi casi di studio offrono un'idea di come gli interventi sulle piccole e medie imprese di diversi settori possano determinare un aiuto importante dal punto di vista dell'ottimizzazione dei processi aziendali.
Anche se le sfide specifiche possono variare, i principi di base dell'ottimizzazione dei processi aziendali rimangono universali per le PMI che vogliono prosperare nell'attuale panorama competitivo.
In conclusione, la strada per il successo aziendale spesso implica la volontà di adattarsi, innovare e ottimizzare continuamente i processi.
Investendo nell'ottimizzazione dei processi aziendali si possono avere ritorni significativi, garantendo la vitalità e il successo in vari settori.